Bike industry leaders use Complam recycled carbon fiber for injection molding, composite lamination, thermoforming and compression molding.
Switching to using recycled carbon fiber components as an alternative to thermoset carbon fiber and plastic components adds significant benefits to differentiation and sustainability goals for greener bicycle manufacturing. This message from Eurobike 2022 is increasingly important to bike manufacturers as we head to Eurobike 2023.
Complam leads in closed loop carbon fiber recycling for sustainable manufacturing from recycled carbon fiber. We are able to manufacture compression molded structural components for bikes as well as injection molding resin and thermoformable laminates. See our products on stand Messe Frankfurt hall 9.2 / C2
Three unique selling points of recycled carbon fiber
Using recycled carbon fiber in bicycle component manufacturing generates three significant unique selling points (USP) that can be used to build market leadership and brand recognition:
- Establishing market differentiation with recycled carbon fiber
- Market leadership through adopting recycled carbon fiber technologies
- Environmentally friendly brand image
Establishing market differentiation with recycled carbon fiber
The use of recycled carbon fiber components sets a company apart from competitors by demonstrating a commitment to sustainability and environmental responsibility. This attracts environmentally conscious customers.
Market leadership through adopting recycled carbon fiber technologies
Adopting recycled carbon fiber technology for carbon fiber component manufacturing demonstrates corporate leadership in adopting innovative and sustainable technologies, adding to brand reputation and credibility in the marketplace.
Environmentally friendly brand image
Including recycled carbon fiber in previously hard to recycle carbon fiber products enables a company to promote its brand as environmentally friendly, forward-thinking, and socially responsible. This improves customer loyalty and retention, and adds positive associations to corporate branding.
Manufacturing with recycled carbon fiber focuses attention on sustainability.
Making the switch to recycled carbon fiber components creates competitive advantage in the market, adds to sustainability targets, and contributes to a more environmentally responsible and resource-efficient future economy.
There are four key ways in which manufacturing with recycled carbon fiber promotes sustainability in both local and global terms:
- Conservation of resources
- Reducing waste
- Energy efficiency
- Driving a circular economy
Conservation of resources
Recycling carbon fiber uses less energy and raw materials, and produces much lower carbon emissions than new carbon fiber production. Companies can contribute to conserving natural resources and reducing carbon emissions associated with manufacturing processes by utilizing recycled carbon fiber.
Reducing waste
The environmental impact of disposing of carbon fiber waste in landfills is a significant, and increasing, problem. Carbon fiber production waste as well as end of life carbon fiber products can be recycled and reused to manufacture new products.
Energy efficiency
Manufacturing recycled carbon fiber components requires less energy than producing new carbon fiber from raw materials. This reduces carbon emissions and results in a smaller carbon footprint for the company.
Driving a circular economy
The principles of a circular economy are founded on recycling and reuse of materials to manufacture new products. Switching to recycled carbon fiber is a way to increase the useful lifespan of carbon fiber materials, save energy and raw materials, and minimize waste.
Complam manufactures GRS certified recycled carbon fiber products
Our carbon fiber recycling facility reclaims fibers from production waste or end of life thermoset carbon fiber that is usually disposed of in landfill as too difficult to recycle. We then reuse the reclaimed fibers and resin in new products made from recycled carbon fiber (RCF) without compromising performance or appearance.
Complam leads in three innovative technologies for sustainable carbon fiber manufacturing from recycled carbon fiber. We are able to manufacture compression molded structural components for bikes as well as manufacturing injection molding resin and thermoformable laminates at our GRS certified facility in Taiwan.
What are Complam’s 3 innovative sustainable carbon fiber manufacturing technologies?
- Compression molding of die-cut recycled carbon fiber composite laminates
- Thermoformable composite laminates made from recycled carbon fiber
- Recycled carbon fiber injection molding resin
Compression molding of die-cut recycled carbon fiber composite laminates
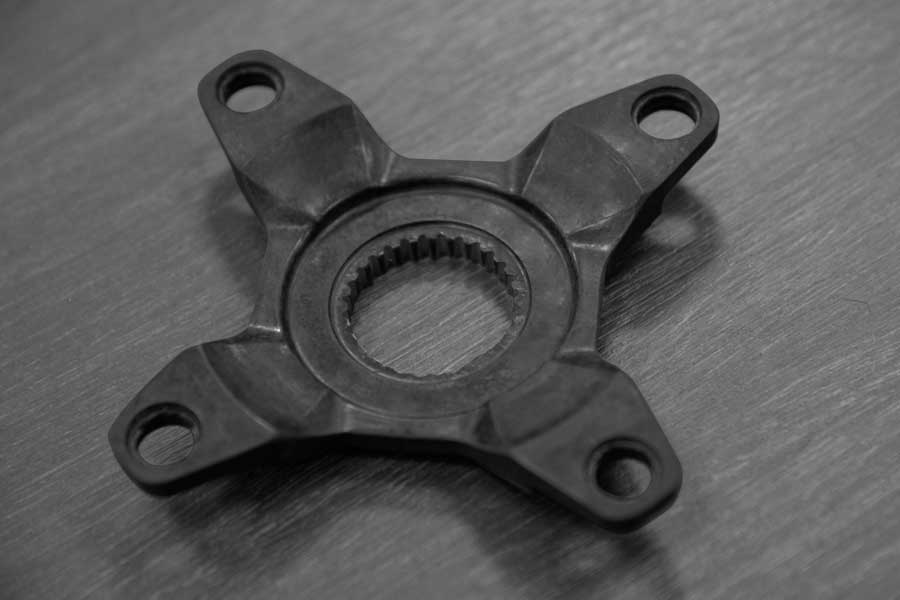
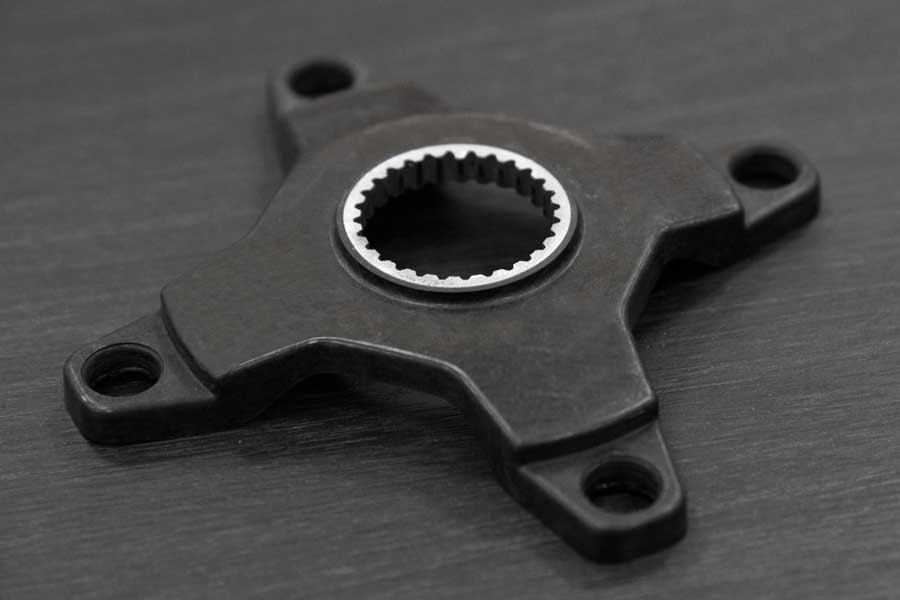
Precision die-cut laminates manufactured from 100% recycled carbon fiber materials are compression molded to produce structurally robust components. Alloy inserts can be included for increased rigidity and structural strength. The bicycle chain spider pictured here offers an example of a sustainable, practical use of this carbon fiber manufacturing process.
Thermoformable composite laminates manufactured from recycled carbon fiber
Global cycling component manufacturers such as SRAM are working with Complam to offer a thermoformed bicycle fender with astonishing sustainability credentials. This revolutionary product is manufactured with 100% recycled carbon fiber recovered by Complam’s carbon fiber recycling process. Complam thermoformable composite laminates offer a sustainable alternative to existing carbon fiber bicycle components.
Recycled carbon fiber injection molding resin
Our recycled injection molding resin contains 12%-20% recycled carbon combined with Ocean Plastic recovered PA66. This blend can be used in standard injection molding machines without retooling, process changes or material behaviour issues. Another remarkable success story from our carbon fiber recycling program.
Sustainable carbon fiber manufacturing & closed loop recycling
Reclaimed carbon fiber (RCF) can be used to manufacture structural and non-structural components. We operate a closed-loop carbon fiber recycling facility that reclaims carbon fibers from thermoset carbon fiber waste. The sustainability of our recycling systems has been demonstrated in recycling bike frames and components.
When you are competing for consumer attention in a competitive market, you need to have the certification to demonstrate your global leadership in sustainability. The CompLam facility in Taiwan which manufactures exclusively thermoplastic carbon fiber is certified to ISO 14067:2018 Greenhouse Gases, Global Recycled Standard, and the ISO 14064 CO2 Verified standard.
In the bike industry, Complam carbon fiber laminates are used to manufacture fenders, seats, E-motor covers, parts and battery enclosures as well as bike chainring spiders. We enable manufacturers to demonstrate their sustainable credentials without compromising on quality or performance.
Customizable composite laminates from Complam
At Complam we manufacture composite laminates with organic or glass fiber reinforcement as well as a wide range of customizable carbon fiber laminates. All our products are customizable to achieve almost any finish and meet a wide range of engineering standards.
- Reclaimed carbon fiber pelletized for injection molding
- Reclaimed & new carbon blends
- Fiber reinforcement with organic flax
- Reclaimed non woven carbon felt
New to reclaimed carbon fiber proportions can be modified to meet your design and product specification. We manufacture injection molding pellets with between 12% and 20% recycled content. Composite laminates for compression molding and thermoforming can be manufactured from up to 100% recycled materials.